Решаването на проблема с ефективността на процеса има два положителни ефекта.
На първо място, въвеждането на обработка с бобина в процеса – както видяхме – води до спестявания на суровини, които дори могат да надхвърлят двадесет процента за същото количество продукт и това означава положителни маржове и паричен поток, който е незабавно достъпен към компанията.
Това може да варира в зависимост от сектора и употребата: във всеки случай това е материал, който предприемачът и компанията вече не трябва да купуват и отпадъците също не трябва да се управляват или изхвърлят.
Целият процес е много по-печеливш и положителният резултат се вижда веднага в отчета за доходите.
Освен това, закупувайки по-малко суровини, компанията автоматично прави процеса по-устойчив, тъй като тази суровина вече не трябва да се произвежда надолу по веригата!
Енергийната ефективност е друг важен елемент в цената на всеки производствен цикъл.
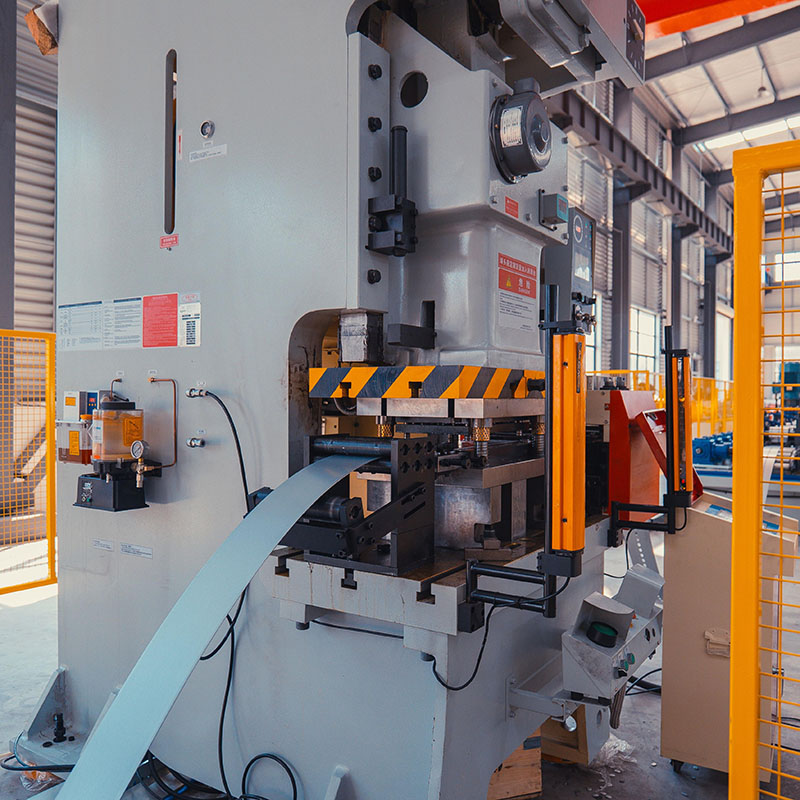
В една модерна производствена система потреблението на машина за формоване на руло е сравнително ниско.Благодарение на системата Combi, линиите могат да бъдат оборудвани с няколко малки двигателя, задвижвани от инвертори (вместо един голям специален двигател).
Използваната енергия е точно тази, необходима за процеса на формоване, плюс всякакво триене в трансмисионните части.
В миналото голям проблем с машините за бързо рязане беше енергията, разсейвана през спирачните резистори.Наистина, режещият блок се ускорява и забавя непрекъснато, с голям разход на енергия.
В днешно време, благодарение на модерните вериги, можем да натрупваме енергия по време на спиране и да я използваме в процеса на формоване на ролката и в последващия цикъл на ускоряване, като възстановяваме голяма част от нея и я предоставяме на системата и на други процеси.
Освен това, почти всички електрически движения се управляват от цифрови инвертори: в сравнение с традиционно решение, възстановяването на енергия може да достигне до 47 процента!
Друг проблем по отношение на енергийния баланс на машината е наличието на хидравлични задвижващи механизми.
Хидравликата все още изпълнява много важна функция в машините: в момента няма серво-електрически задвижващи механизми, способни да генерират толкова много сила в толкова малко пространство.
Що се отнася до машините за щанцоване със спирално захранване, в първите години използвахме само хидравлични цилиндри като задвижващи механизми за щанцовете.
Машините и нуждите на клиентите продължиха да растат, както и размерът на хидравличните агрегати, използвани в машините.
Хидравличните силови агрегати поставят маслото под налягане и го разпределят по цялата линия, с последващи спадове в нивата на налягане.
След това маслото се нагрява и се губи много енергия.
През 2012 г. представихме на пазара първата сервоелектрическа машина за щанцоване със спирално захранване.
На тази машина заменихме многото хидравлични задвижващи механизми с една електрическа глава, управлявана от безчетков двигател, който развива до 30 тона.
Това решение означава, че енергията, необходима на двигателя, е винаги само тази, необходима за рязане на материала.
Тези серво-електрически машини също консумират 73% по-малко от подобни хидравлични версии и също така осигуряват други предимства.
Наистина, хидравличното масло трябва да се сменя приблизително на всеки 2000 часа;в случай на течове или счупени тръби отнема много време за почистване и повторно пълнене, да не говорим за разходите за поддръжка и проверките, свързани с хидравличната система.
Въпреки това, сервоелектрическото решение изисква само презареждане на малкия резервоар за смазка и машината може да бъде напълно проверена, дори дистанционно, от оператор и сервизен техник.
В допълнение, серво-електрическите решения предлагат около 22% по-бързо време за изпълнение в сравнение с хидравличната технология. Хидравличната технология все още не може да бъде напълно елиминирана от процесите, но нашите изследвания и разработки със сигурност са насочени към все по-широко разпространеното използване на серво-електрически решения поради множество предимства, които предоставят.
Време на публикуване: 23 март 2022 г